In the oil, gas, petrochemical, and refineries industries, due to the presence of flammable gases and liquids, the risk of explosion and fire is very high. The occurrence of such incidents can lead to many human and financial losses. For this reason, it is necessary to constantly monitor gas leaks and the presence of flames in these industries. This necessity determines the importance of F&G System in these industries.
In the previous articles of Ganjineh Pavan, we discussed the design of the F&G system for flame and gas detection and its challenges. In this article, we intend to discuss the importance and necessity of the Fire and Gas Detection System in the oil, gas, and petrochemical industry.
Types of oil and gas industry risks and the importance of F&G system
The process of extracting, transporting, processing, and refining oil and gas is complex and dangerous for workers and assets. One of the most dangerous of them is the risk of fire or explosion due to the presence of flammable gases and liquids. Toxic gases and chemicals encountered during the processes increase the risk of suffocation, burns, cancer, and system corrosion.
To reduce risks to life, property, or the environment, oil and gas companies follow mandatory safety practices. Portable and fixed gas detection systems and flame detection systems play an important role in detection the environment for hazards. In addition, respirators or other safety equipment can be provided to workers to keep them safe.
The good news is that the oil and gas industry has fewer safety incidents today than in the past as a result of understanding and addressing hazards through mandatory regulations.
Risk of fire and explosions in oil and gas industries
The oil and gas industry is usually divided into three main segments: upstream, midstream, and downstream.
Getting a reliable early warning about the possible risk of explosion or fire is one of the main demands of the petrochemical, gas, oil, and fuel industries in general and offshore platforms in particular.
Fuel leaks, the presence of flammable liquids with low flash points, and the formation of volatile vapor clouds that travel along dense pipelines and hot production zones may accumulate in confined areas (traps). Or mix with air and form a mixture of flammable fuel and air, which causes fire and even explosion in the presence of an ignition source. This high probability of fire and explosion risk in the oil, gas, and petrochemical industry reveals the necessity and importance of the F&G system or the fire and gas detection system in these industries.
Like other process industry operations, oil and gas terminals pose difficult challenges for automation and safety technology. Tank farms, storage areas, and loading/unloading operations all require fire, gas, and safety systems to protect personnel, assets, and the environment. The consequences of accidents in oil and gas terminals can be very high.
Buncefield fuel terminal explosion
Failure caused by failure to properly design, install, operate, and maintain the Fire and Gas System or FGS can be better explained with real examples.
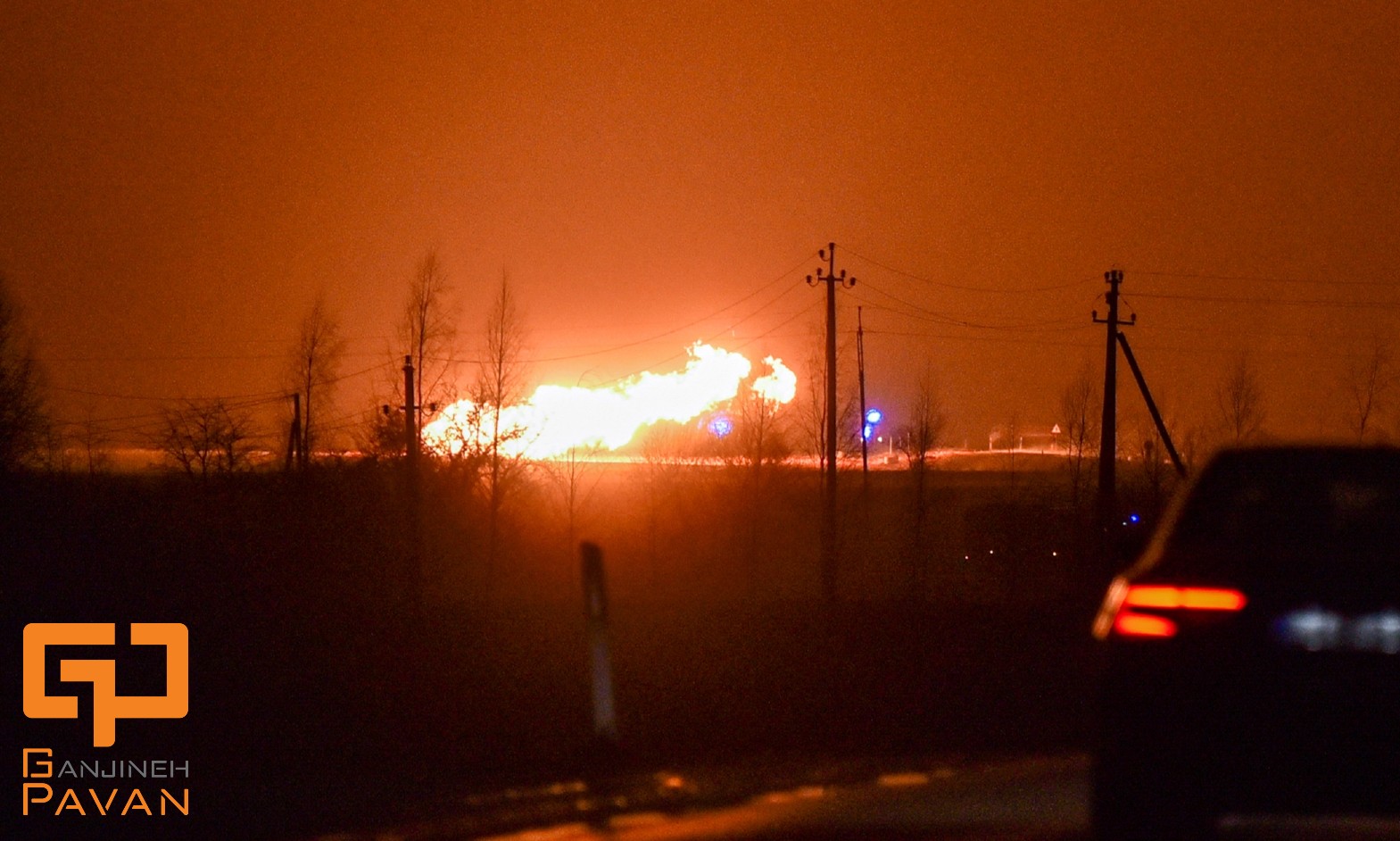
In December 2005, an explosion at the Buncefield fuel terminal in Hertfordshire, UK ignited millions of gallons of fuel. Water and land quality across southern England was adversely affected, and clean-up operations cost hundreds of millions of pounds.
Fire in Tehran Oil Refining
Among the domestic incidents in this field, we can mention the fire of a part of the Fire in Tehran Oil Refining due to a tank leak on June 2, 2021. This fire was extinguished with 24-hour efforts of fire brigade officers and no casualties. However, if the fire spreads to the LPG tank of this refinery, it could cause destruction equivalent to an 8-magnitude earthquake.
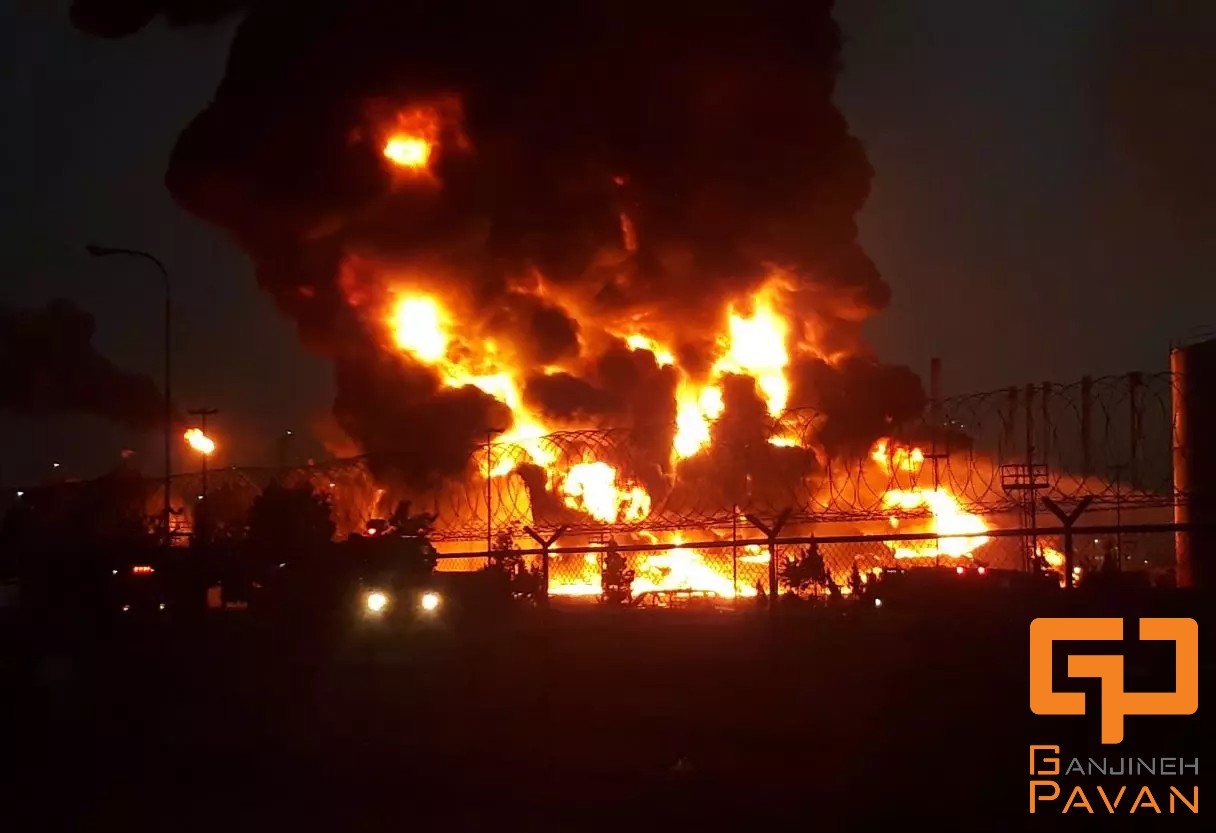
Incidents such as the Bancefield terminal fire or the Tehran Oil Refining fire show potential threats to the oil and gas supply chain in Iran and around the world and other critical process industry sources. Comprehensive solutions that address both safety and security in these facilities are needed.
The role of fire and gas detection system (F&G System) in controlling and reducing risk
Fire and gas (F&G) detection and mitigation systems are key to maintaining the safety and overall performance of industrial facilities. The scope of application of F&G systems includes offshore oil exploration and production, onshore oil and gas facilities, refineries and chemical plants, marine operations, tank farms and terminals, pipelines, power plants, mining, and paper mills.
The importance of F&G system or flame and gas detection is that this system continuously monitors abnormal conditions such as fire or release of combustible or toxic gases in these industries. And provides early warning and mitigating actions to prevent escalation of the incident and protect the process or environment.
The importance of an integrated fire and gas safety and detection strategy
By implementing an integrated fire and gas strategy based on the latest automation technology, these industries can meet their environmental safety and critical infrastructure protection requirements while ensuring operational and business readiness at project start.
The Safety Shutdown System is a preventive safety layer that takes automatic and independent action to prevent a dangerous accident and protect personnel and plant equipment from potentially serious damage. On the contrary, the Fire, and Gas Detection System is a mitigating safety layer that is responsible for reducing the consequences of a dangerous event after its occurrence.
For example, in oil and gas terminal applications, operators need an integrated fire and life safety system that enables proactive response to alarms and events and a real-time view of any potential threat. Industrial plants have safety procedures and systems designed to bring operations to a safe state in the event of equipment failure and other operational problems. In the event of a major security incident, an integrated system can activate these same procedures and systems. An integrated system also results in less expensive implementation and maintenance because all parts work together.
New developments in F&G gas and flame detection system technology
An F&G safety system includes detection, logic control, and warning and mitigation functions. The logic solver is the central control panel unit of the F&G system. The controller receives alarm and status or analog signals from field detection devices required for fire and gas detection. The controller takes the necessary actions to initiate the warning and reduce the risk.
Fire and gas detection devices, including flame detectors and gas detectors, have made great progress in recent years. Using new techniques and adding intelligence to these tools to reduce the number of false alarms has greatly improved the detection rate. The correct and proven connection of fire and gas detectors to industrial safety systems is an important factor in the reliable operation of the F&G system and to achieve the desired safety integrity level (SIL).
In the past, dedicated F&G systems were either stand-alone equipment or a wired emulation overview panel via relays. In these systems, the risk reduction was done through manual activation of fire control measures. Today, F&G detection systems are generally programmable electronic systems (PES) with high safety capability and reduced effectiveness. As modern F&G systems are tightly integrated with the overall process safety strategy, mitigation is either through an emergency shutdown (ESD) system or directly from the F&G system itself.
Importance of F&G system to control and reduce common risks in oil and gas refineries
The oil and gas refining process creates several potential hazards due to the presence of various chemicals and flammable gases and liquids. In addition to the risks of industrial exposure to chemicals and accidents such as fire and explosions, there are health risks caused by air pollutants. Which may be part of the normal refining process. Or it can occur unexpectedly in an oil refinery.
Crude oil contains thousands of hydrocarbons and other chemicals that may cause short-term and long-term health problems, corrosive burns, or suffocation in refinery workers. Therefore, gas and flame detection and the necessity and importance of the F&G system in different units of a refinery are vital aspects. But some specific risks can also be estimated in different units and solutions can be sought for them.
Dangers of confined spaces in Oil and gas refineries
Entering confined spaces is common in refineries. Because there are many sets of tanks, reactors, vessels, and ducts. Many workers have lost their lives due to not observing necessary precautions and having proper equipment before entering a closed space.
The potential dangers of these spaces include lack of oxygen, and leakage of gases such as H2S, SO2, NO2, NH3, CO, HCl, Cl2, and H2. These risks reveal the critical aspect and importance of the F&G system in these spaces.
Importance of F&G system to control hot work hazards
Hot work includes welding, soldering, cutting, grinding, soldering, and melting, which causes heat, sparks, and hot slag. These activities may ignite flammable and combustible materials in the area of said activities. If the work and equipment are not located outside the hazardous areas, precautions should be taken to increase safety.
The working atmosphere is monitored with a gas detector before the start of hot work and is usually re-evaluated during the work. Hot work done in a confined space must also follow specific confined space regulations. The potential hazards of these works are the presence of H2S and flammable gases.
Common hazards of repair, maintenance, and shutdown operations
Maintenance operations are planned as part of normal operating processes, maintenance, and cleaning of processing and storage units. Companies spend considerable time planning for such events so that they can perform maintenance as quickly as possible to minimize downtime.
In any case, refineries usually use service companies that bring contractors to the site to do the work. These contractors are equipped with personal protective equipment (PPE), including portable gas detectors, to use during maintenance.
Fire and gas detection system technologies
In safety applications, gas detection should be used to warn of the presence of a dangerous amount of gas in an area. Often it is not important to detect a local leak. Because it is either too small to threaten safety. Or it may cause a sudden fire. With proper fire risk management, it can be identified and extinguished in time.
There are several technologies that can be used to deploy a fire and gas detection system to detect gases in oil and gas refineries. Electrochemical sensors are used to monitor the amount of oxygen in the air or the presence of toxic gases such as CO, H2S, Cl, and Cl2.
Semiconductor sensors are used where there are high concentrations of H2S or high ambient temperatures.
Catalytic and infrared explosion-proof gas detectors are used to detect explosive gases such as CH4 or carbon dioxide (CO2). Infrared IR detectors are also recommended for corrosive atmospheres or where high levels of H2S are present.
Gas detection systems in oil and gas refining
Fixed gas and flame detection systems are used throughout refineries to detect leaks or the presence of toxic or flammable gases. This shows the importance of the F&G system and its vital aspect in these industries.
In F&G system design, the choice of sensors and detectors for detection depends on a careful assessment of potential hazards. While placement and configuration such as an open path detector, fixed point, or a combination of systems help ensure coverage throughout the area while minimizing false alarms.
Portable gas detection systems such as portable gas detectors are used by workers and contractors based on the standard operating method of refineries. Typically, gas detectors are used in all areas deemed potentially hazardous.
As multi-gas detection detectors decrease in size, many refineries are replacing single-gas detectors. There are certain applications such as confined spaces that require the use of portable gas detectors to comply with regulations.
Flame detection technologies in oil and gas industries
The petrochemical industry and especially the offshore industry are well aware of the high risk of some processes and necessary safety procedures, including the importance of the F&G system to protect expensive and sometimes irreplaceable equipment and personnel.
Current fire risk management includes Triple IR optical explosion-proof flame detector technology that provides very fast and accurate fire detection. This technology uses the infrared emission spectrum of flames. And analyzes it against background radiation using 3 selectable IR channels. The following flame detection review summarizes existing flame detection technologies, their limitations, and future trends.
UV flame detectors are absorbed by air, smoke, dust, gases, and various organic substances in the surrounding atmosphere due to their short-wave characteristics. Therefore, atmospherically scattered U.V. solar radiation, especially at wavelengths shorter than 300 nm (solar-blind spectral band) absorbed by the surrounding atmosphere, will not cause false alarms for flame detectors using this technology.
Ganjineh Pavan Company; Consultant, designer, supplier, and implementer of F&G systems in the oil and gas industry
Ganjineh Pavan Company provides consulting, design, supply, implementation, integration, commissioning, and maintenance services in the field of safety, notification, and fire extinguishing of oil, gas, petrochemical, and refining industries.
Among the projects of Pawan’s treasure in this field, the following can be mentioned:
- National Iranian Oil Engineering and Construction Company
- Bistoon petrochemical company
- Lavan Oil Refining Company
- Kaveh Methanol Company
To receive a free consultation in the field of design, supply, and implementation of various safety and fire protection projects in various industries, including oil, gas, and petrochemicals, contact our experts in Ganjineh Pavan .
:References